
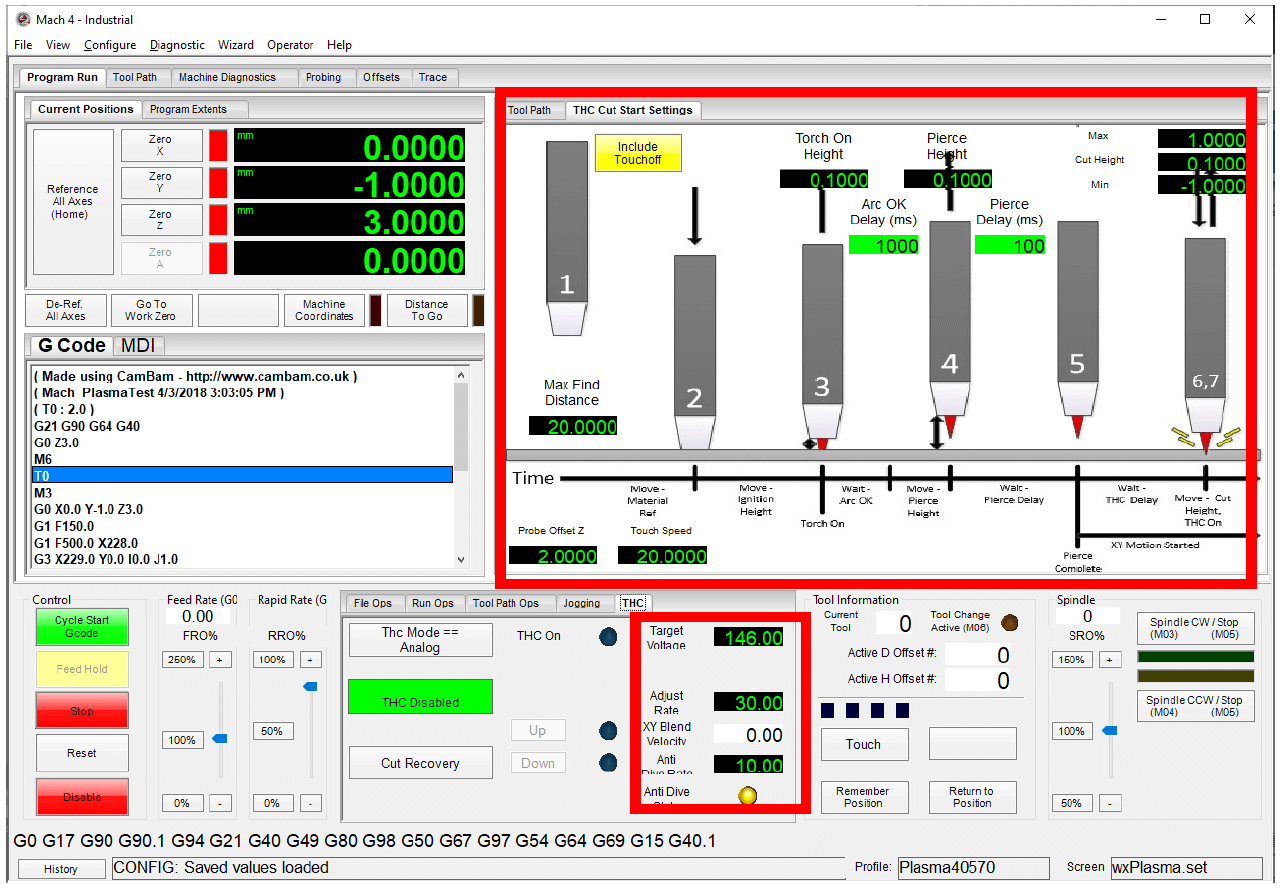
I’ll be testing MeshCAM on Linux shortly as well. As mentioned CamBam has a version that using Mono on Linux, and I have run some simple tests using that installation and it appears to work fine. MeshCAM is supposed to run under Linux using Wine and they have a web page dedicated to setting it up under Wine.
#Cambam cnc tab plus
I don’t know yet if I could say that the 3D processing is good enough, but will be testing is some more over the next few days.īoth MeshCAM and CamBam have very responsive forums so that is a BIG plus when you need answers to questions about the software, or CNC in general. CamBam has a good UI, and gives you a good amount of control. MeshCAM is a bit easier since it is more automatic, but if there are issues with the STL file that could impact the resulting gcode. I wish that MeshCAM and CamBam had the same feature set, but then don’t so I’ll have to choose one of them.
#Cambam cnc tab free
If I can free up some time I may help with debugging and adding features. Depending on the state of the nightly build there may be bugs, and as things change sometimes the docs and notes are not catching up. It is integrating some of HeeksCNC processing into FreeCAD and it is coming along pretty well, and is usable for simple jobs. I used the ShapeOko post processor since that is GRBL based and it works well with GRBL 0.9 as wellįreeCAD - daily build Path Workbench. DXF is for people who wanted to do simple plates with holes in them according to the MeshCam forum. So you have to use the STL files for 3D milling for sure. Unlike with CamBam or Estlcam where you can specify outlines and then set the depth for each. All holes go all the way though if you are importing DXF.
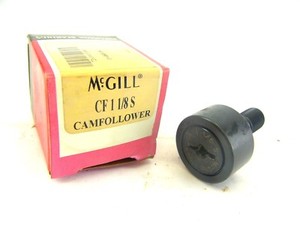
Note: MeshCam can import DXF files but there is no way to specify pocket operations from the DXF. MeshCam, if more STL model file tests are good then MeshCam will probably move to the top of my list. I’m running another test with settings tweaked to add the support tabs and cutting the milling time in half, so I’ll know more when it completes. The slot and rectangle pockets were properly milled, and the 8mm hole with 2mm chamfer from the model milled OK. But MeshCam generated gcode that appears to be perfect directly from the STL. Was going to take a long time to complete and I forgot to add support tabs, so I stopped it before the final finishing run. Took the default rough and finish settings with my end mill for the tool. MeshCam - Did a test using the same STL as with Estlcam and CamBam. With CamBam I used the LinuxCNC post processor and it is working well with GRBL v0.9 $150US I need to revisit the STL test now that I’ve gotten more experience with CamBam and seen how MeshCam works. A couple of minor GUI issues, but non critical. CamBam has a version that runs on Linux using Mono, and it looks pretty good. For fun I did a chamfer on one of my test holes and it milled perfectly.
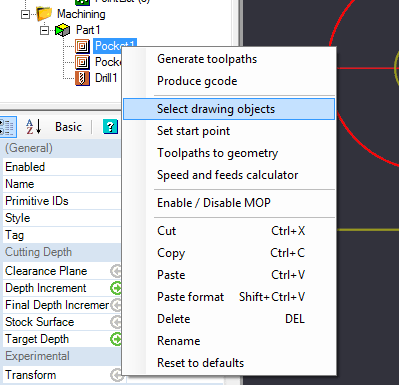
CamBam supports side profile operations which is nice. CamBam produced something that was looking good, but I didn’t have something configured correctly so I stopped the test before it completed and switched over to using a DXF file and specifying Pocket and Profile operations. I did an initial test using the exact same STL file that I used with Estlcam test.
#Cambam cnc tab manual
Didn’t matter if I used the automatic 3D functionality or the manual process, didn’t produce anything close to the model.ĬamBam - I’ve produced some accurate pieces in foam and really like a lot about CamBam. For the STL of my test model Estlcam produced junk for the gcode. It seems to work for others so some of it is probably just being new to the CNC world. I’ve been testing several different low cost CAM packages with my MPCNC:ĮstlCam - I found a number of issues that for me make it a non-starter, and unfortunately didn’t get responses to my questions to assist with moving forward with the purchase.
